Koreas größtes Forschungslabor glänzt mit nachhaltiger Glasarchitektur
Im Westen der Millionenmetropole Seoul bündelt der weltweit aktive Konzern LG seine Abteilungen für Forschung und Entwicklung. Im neuen LG Sciencepark sind bereits rund 22.000 Mitarbeiter tätig und entwickeln Lösungen für ein neues Zeitalter im Zeichen der Digitalisierung und der Industrie 4.0. Auf dem Campus sind unter der Federführung des international tätigen Architekturbüros HOK bisher 20 Gebäude entstanden. Teil der nachhaltig konzipierten und LEED-zertifizierten Forschungszentren sind die hochwertigen Glasfassaden mit dem Warme-Kante-System Ködispace 4SG von H.B. Fuller | KÖMMERLING.
Die LG Group mit ihren Tochtergesellschaften, wie LG Electronics oder LG Hausys, gehört zu den weltweit größten Konzernen. Das 1947 gegründete Unternehmen beschäftigt weltweit über 200.000 Mitarbeiter und hat seinen Firmensitz in der südkoreanischen Hauptstadt Seoul. Bis 2018 waren die Abteilungen für Forschung und Entwicklung der Tochterunternehmen über die ganze Metropole verteilt. Mit dem neuen LG Sciencepark bündelt der Konzern seine Forschungslabore an einem Ort. Auf einer Gesamtfläche von 170.000 Quadratmetern entsteht im Westen Seouls eine Gebäudestruktur, so groß wie eine deutsche Mittelstadt – für bis zu 25.000 Mitarbeiter. Der Campus ist damit Koreas größtes Wissenschaftszentrum.
Innovationen für ein besseres Leben
Im LG Sciencepark wird an neuen Technologien wie künstlicher Intelligenz, Robotik, autonomem Fahren oder an neuen Innovationen für ein effizientes Energiemanagement, erneuerbaren Energien oder Biotechnologien geforscht. Damit neuartige, revolutionäre Ideen entstehen, wünschte sich LG eine inspirierende Umgebung für seine Forscher. Der Campus soll die Teamarbeit und die Lust am Entdecken fördern und flexibel auf sich ändernde Raumanforderungen reagieren können. In enger Zusammenarbeit mit LG konzipierte das Architekturbüro HOK den Sciencepark unter dem LG-Slogan „innovation for a better life“. Bis 2024 sollen auf dem Campus 26 Gebäude entstehen, fertiggestellt sind aktuell 20. Für jede Tochtergesellschaft steht ein individuell gestaltetes Haus mit jeweils neun Stockwerken zur Verfügung, mit eigenem Eingang und großzügigem Foyer. Untereinander verbunden sind die Einheiten mit begrünten Fußgängerpromenaden, die zum Verweilen und zum Austausch einladen. Auch mehrere eingeschossige Brückengebäude verbinden die einzelnen Häuser. Diese spenden dem Erdgeschossniveau Schatten, auf ihren begehbaren Dächern wurden wiederum kunstvoll gestaltete Gärten angelegt.

Hightech-Gläser für den Sciencepark
Rund 98.000 Quadratmeter Glas wurden auf dem Campus bisher verbaut – das entspricht der Fläche von fast 14 Fußballfeldern. LG konnte für das verwendete Zweischeiben-Isolierglas auf das bewährte Low-E-Glas der Konzerntochter LG Hausys zurückgreifen. Seit rund zehn Jahren fertigt LG Hausys das sogenannte Low-Emissivity-Glas, auf das eine hauchdünne Metallschicht aufgebracht wird. Dieser Auftrag reduziert den Emissionsgrad der Verglasung und dient als Wärme- und Sonnenschutzschicht.
Langlebiger Randverbund
LG Hausys gilt als Innovationstreiber der Baubranche und setzt als bisher einziger Isolierglashersteller in Südkorea das hochwertige Warme-Kante-System Ködispace 4SG von H.B. Fuller | KÖMMERLING ein. Der thermoplastische Abstandhalter für Isoliergläser bietet bei einer einzigartigen Optik höchste Energieeffizienz und maximale Lebensdauer und entspricht voll und ganz den hohen Ansprüchen von LG. Denn Glasfassaden wie die im LG Sciencepark müssen den thermischen Belastungen dauerhaft standhalten können. In Seoul sind die Winter kalt und die Sommer heiß. Damit die Isoliergläser diese Temperaturunterschiede verarbeiten können und ihre Energieeffizienz erhalten bleibt, ist ein dauerhaft funktionierender und dichter Randverbund unbedingte Voraussetzung. Isoliergläser mit dem elastischen Abstandhalter Ködispace 4SG haben sich als außerordentlich robust, belastbar und langlebig erwiesen. Die Warme-Kante-Lösung erfüllt jedoch nicht nur auf einzigartige Weise die Anforderungen an einen dauerhaft dichten Randverbund, sondern ist auch unter gestalterischen Aspekten hochinteressant. Denn die Applikation des reaktiven thermoplastischen Abstandhaltersystems erfolgt vollautomatisch, weswegen Isoliergläser mit Ködispace 4SG absolut präzise und optisch perfekt produziert werden können. Dadurch entwickeln diese Gläser eine einzigartige Ästhetik: kein unschöner Versatz der Abstandhalterprofile und vor allem keine störenden Lichtreflektionen wie bei klassischen Abstandhaltersystemen – das schwarze Ködispace 4SG macht den Scheibenzwischenraum praktisch unsichtbar.



Zertifizierte Nachhaltigkeit
Das US-amerikanische Architekturbüro HOK (Hellmuth, Obata + Kassabaum) mit weltweit über 1.600 Mitarbeitern hat zusammen mit dem lokalen Partnerbüro Gansam Architects eine sehr nachhaltige Architektur für den Wissenschaftscampus konzipiert. Im Vergleich zu den bisher über die Stadt verteilten Gebäudeeinheiten konnte der Energieverbrauch um 38 Prozent gesenkt werden. Der LG Sciencepark wurde nach dem Nachhaltigkeitsstandard LEED des U.S. Green Building Council zertifiziert. Die Forschungsgebäude erhielten die Auszeichnung Silver, das Integrated Support Center (ICS) erreichte mit Platinum sogar das höchste Niveau. Das ICS steht im Herzen des Campus, dient unter anderem Veranstaltungen, Ausstellungen und Seminaren und enthält Kindertagesstätten sowie Sport- und Erholungsbereiche. Auch von der Korea Energy Agency wurde der Campus als „Energy Champion“ ausgezeichnet. Einen großen Anteil am Energiekonzept haben neben Photovoltaik-Anlagen und Grundwasser-Wärmepumpen die hochwärmegedämmten Fassaden mit ihren großzügigen Glaselementen.



Die Isoliergläser von LG Hausys mit dem Warme-Kante-System von H.B. Fuller | KÖMMERLING tragen beim Sciencepark zur hochwertigen und nachhaltigen Architektur maßgeblich bei. Zudem versorgen die großzügigen Glasfassaden die Gebäude mit viel Tageslicht und generieren lichtdurchflutete Labore und Büroräume für die Mitarbeiter des Wissenschaftscampus. „Alle Design-Entscheidungen wurden aus der Perspektive der Forscher getroffen – mit dem Fokus auf Produktivität und dem Austausch zwischen den Forschenden. Hier wird LG die Zukunft für die Menschheit entwerfen“, erklärte Ju-Hwan Shin, Managing Director LG Sciencepark Business Unit/Construction Drive Division, bei der Eröffnung des LG Sciencepark.
Über die Kömmerling Chemische Fabrik GmbH
Seit 2017 ist die Kömmerling Chemische Fabrik GmbH als H.B. Fuller | KÖMMERLING Teil des US-amerikanischen Klebstoffkonzerns H.B. Fuller. Der weltweit größte Anbieter von Kleb- und Dichtstoffen für Isolierglasanwendungen verfügt damit über eine bedeutende Expertise in diesem Bereich, die bei H.B. Fuller | KÖMMERLING am deutschen Standort Pirmasens durch Forschungen und neue Anwendungsfelder stetig vorangetrieben wird. Insgesamt deckt H.B. Fuller mit den drei Geschäftsfeldern Engineering Adhesives, Construction Adhesives sowie Hygiene, Health and Consumable Adhesives vielseitige und hochwertige Kleb- und Dichtstoffanwendungen ab, die in einer Reihe von Branchen wie Elektronik, Hygiene, Medizin, Transport, Bau und Erneuerbare Energien eingesetzt werden. Der internationale Konzern erzielt einen Umsatz von rund 3 Milliarden US-Dollar und betreut mit 6.500 Mitarbeitern Kunden in mehr als 125 Ländern.
Weitere Informationen und Belegexemplar an:
Kömmerling Chemische Fabrik GmbH
Alexandra Rohr
Zweibrücker Str. 200
D-66954 Pirmasens
Bildnachweis: H.B. Fuller | Kömmerling
Moderne Glasarchitektur stellt extreme Anforderungen an die dauerhafte Energieeffizienz und Gasdichtigkeit der Isoliergläser. Mit Ködispace 4SG bietet der Kleb- und Dichtstoffhersteller Kömmerling ein bewährtes und besonders leistungsfähiges Warme-Kante-System, das sich optimal für anspruchsvolle Structural-Glazing-Projekte eignet – wie die beeindruckende Shoppingmall Chadstone in Australien.
Auf dem schmalen Grat zwischen Form und Funktion müssen Glasfassaden heute scheinbar unumstößliche physikalische Grenzen sprengen. Was bereits realisierbar ist, zeigt das gewagt fließende Glas-Stahl-Dach der Mall Chadstone in Melbourne. Die dreidimensionale Form der über 7.000 qm großen Dachkonstruktion ergibt sich aus Stahlknoten, Stäben und Randträgern. Sie tragen 2.672 kaltgebogene Isolierglaseinheiten mit dem thermoplastischen Abstandhalter Ködispace 4SG als Warme-Kante-System.
Keine einzige der zwischen 1,2 und 8 qm großen Isolierglaseinheiten ist mit einer der anderen identisch, da jede sich anders an die organische Gebäudeform anpassen muss. Dazu wurden die 39 mm dicken Zweifach-Isoliergläser bei der Montage an Ort und Stelle in ihr jeweiliges Profil kaltgebogen und fixiert. Durch das Kaltbiegen verformt sich auch der Randverbund. Das kann bei herkömmlichen Abstandhaltern leicht zu Undichtigkeiten im Scheibenzwischenraum führen. Die Warme Kante mit Ködispace 4SG kompensiert dagegen die auftretenden Deformationen wesentlich besser als starre Abstandhaltersysteme, denn das reaktive Polyisobutylen verbindet sich chemisch sowohl mit der Glasoberfläche als auch mit der Silikondichtungsmasse, wodurch der gesamte Randverbund zu einer flexiblen und belastbaren Einheit „verschmilzt“.
Die hohe Belastbarkeit des Abstandhalters wurde neben experimentellen Bauteilversuchen auch durch Finite-Elemente-Simulationen nachgewiesen. So gewährleistet Ködispace 4SG auch bei gebogenen Isolierglaseinheiten eine herausragende Langzeitstabilität und dauerhafte Gasdichtigkeit.
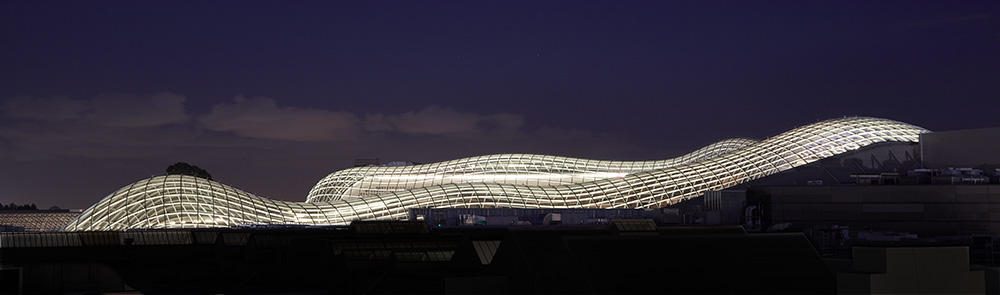


Weitere Informationen und Belegexemplar an:
Kömmerling Chemische Fabrik GmbH
Alexandra Rohr
Zweibrücker Str. 200
D-66954 Pirmasens
Bildnachweis: Kömmerling Chemische Fabrik/Aaron Pocock
Nachhaltige Glasarchitektur im Wahrzeichen von Seoul
Mitten in der koreanischen Millionenmetropole Seoul ragt das World Trade Center als weithin sichtbares Wahrzeichen der Stadt auf. Direkt neben dem charakteristisch stufigen Trade Tower wurde die Silhouette des Gebäudekomplexes um den markanten Parnas Tower erweitert. Teil des nachhaltig konzipierten und LEED-zertifizierten Skyscrapers sind die hochwertigen Glasfassaden mit dem Warme-Kante-System Ködispace 4SG von H.B. Fuller | KÖMMERLING.
Das World Trade Center (WTC) Seoul befindet sich im bekannten Stadtteil Gangnam und ist als größtes Handels- und Geschäftszentrum Koreas eine der Hauptattraktionen für Touristen. Neben dem Trade Tower bieten der ASEM Tower, Bürogebäude, das COEX (Convention & Exhibition) Handels- und Kongresszentrum, angesehene Fünf-Sterne-Hotels und die COEX Mall ideale Räumlichkeiten und Serviceleistungen für Konferenzen, Shopping, Restaurants und Unterhaltung. Internationale Treffen hochrangiger Politiker finden dort ebenso statt wie Wirtschaftsgipfel oder große kulturelle Veranstaltungen.
Höchste Energieeffizienz mit LEED-Gold-Status
Mit dem Parnas Tower haben die internationalen Architekturbüros KMD Architects (USA) und Chang-jo Architects (Korea) dem WTC-Turm ein hochmodernes, energieeffizientes und umweltfreundliches Gebäude
an die Seite gestellt. Der 183 Meter hohe Parnas Tower mit 38 oberirdischen und acht unterirdischen Stockwerken ist ein luxuriöser Büroturm mit modernster Technologie. Die Architekten legten bei der Gestaltung den Schwerpunkt auf eine harmonische Integration in den bestehenden Gebäudekomplex. In Anlehnung an das Designkonzept des benachbarten Trade Tower wurden der südliche untere Teil und der östliche obere Teil des Gebäudes mit transparenten Glaselementen sowie mit diagonalen Vor- und Rücksprüngen gestaltet. Das von KMD entworfene Atrium schafft eine direkte Verbindung zu dem Hotel Grand Intercontinental Seoul Parnas, einer Metro-Station und dem Einkaufszentrum Parnas Retail Mall. Die Lobby im ersten Stock wird durch ein 26 Meter hohes Panorama-Dachfenster erhellt. In jeder Büroetage geben die umlaufenden Verglasungen den Besuchern eine 360-Grad-Aussicht frei und sorgen für lichtdurchflutete Räume.
Mit der Auszeichnung in Gold erhielt der Parnas Tower die zweithöchste Zertifizierung nach dem Nachhaltigkeitsstandard LEED des U.S. Green Building Council. Die hohe Effizienz des Gebäudes wird durch ein ausgeklügeltes Energiekonzept und ein abgestimmtes Gebäudemanagementsystem sichergestellt. Einen großen Anteil an diesem Erfolg haben neben den in die Fassade integrierten Photovoltaik-Anlagen die hochwärmegedämmten, rundum laufenden Glaselemente.
Langlebiger Randverbund im Isolierglas
Rund 25.000 Quadratmeter Isolierglas des Herstellers LG Hausys wurden in der Fassade verbaut. LG Hausys setzt als bisher einziger Isolierglashersteller in Südkorea das hochwertige Warme-Kante-System Ködispace 4SG von H.B. Fuller | KÖMMERLING ein. Der thermoplastische Abstandhalter für Isoliergläser bietet eine einzigartige Optik, höchste Energieeffizienz und maximale Lebensdauer und entspricht daher vollständig den hohen Ansprüchen von LG. Denn Glasfassaden wie die im Parnas Tower müssen den thermischen Belastungen durch die Witterung dauerhaft standhalten können, auch bei extremen Jahreszeiten wie in Seoul. Damit die Isoliergläser diese Temperaturunterschiede verarbeiten können und ihre Energieeffizienz erhalten bleibt, ist ein dauerhaft funktionierender und dichter Randverbund unbedingte Voraussetzung. Isoliergläser mit dem elastischen Abstandhalter Ködispace 4SG haben sich als außerordentlich robust, belastbar und langlebig erwiesen. Die Warme-Kante-Lösung ist zudem auch unter gestalterischen Aspekten hochinteressant. Durch die vollautomatische Applikation des reaktiven thermoplastischen Abstandhaltersystems können Isoliergläser mit Ködispace 4SG absolut präzise und optisch perfekt produziert werden. Das verhilft diesen Gläsern zu einer einzigartigen Ästhetik: kein unschöner Versatz der Abstandhalterprofile und vor allem keine störenden Lichtreflektionen wie bei klassischen Abstandhaltersystemen – das schwarze Ködispace 4SG macht den Scheibenzwischenraum praktisch unsichtbar. Die Isoliergläser von LG Hausys mit dem Warme-Kante-System von H.B. Fuller | KÖMMERLING tragen beim Parnas Tower maßgeblich zur hochwertigen und nachhaltigen Architektur bei.
Partner für innovative Glasarchitektur
Als Partner für innovative Glasarchitektur bietet der Kleb- und Dichtstoffhersteller neben den hochwärmegedämmten Glaselementen darüber hinaus auch Lösungen für fassadenintegrierte Photovoltaik und funktionale Glaselemente. So können beispielsweise komplette Glaselemente für Mediafassaden oder Verbundsicherheitsgläser mit den innovativen LOCA-Systemen (Liquid Optical Clear Adhesives) von H.B. Fuller | KÖMMERLING hergestellt werden.


Über H.B. Fuller | KÖMMERLING
Seit 2017 ist die Kömmerling Chemische Fabrik GmbH als H.B. Fuller | KÖMMERLING Teil des US-amerikanischen Klebstoffkonzerns H.B. Fuller. Der weltweit größte Anbieter von Kleb- und Dichtstoffen deckt mit den drei Geschäftsfeldern Engineering Adhesives, Construction Adhesives sowie Hygiene, Health and Consumable Adhesives vielseitige und anspruchsvolle Kleb- und Dichtstoffanwendungen ab, die in einer Reihe von Branchen wie Elektronik, Hygiene, Medizin, Transport, Bau und Erneuerbare Energien eingesetzt werden. Der internationale Konzern erzielt einen Umsatz von rund 3 Milliarden US-Dollar und betreut mit 6.500 Mitarbeitern Kunden in mehr als 125 Ländern. Der Standort Pirmasens wurde zum „Technology Center of Excellence“ für Isolierglasanwendungen und ist damit für Forschung und Entwicklung neuer Produkte und Anwendungsfelder sowie das Vorantreiben der vorhandenen Expertise verantwortlich.
Weitere Informationen und Belegexemplar an:
Kömmerling Chemische Fabrik GmbH
Zweibrücker Str. 200
66954 Pirmasens
Tel: +49 6331 56-2330
Fax: +49 6331 56-1110
E-Mail: alexandra.rohr@hbfuller.com
www.koe-chemie.de
Bildnachweis: Fotograf: Namgoong Sun
Weitere Informationen für Architekten unter:
https://www.koe-chemie.de/anwendungen-produkte/glas/loesungen-fuer-architekten-und-planer/
Ein Display als Bauelement für Glasfassaden
Hochhaustürme, die direkt in ihrer Fassade ganze Filme abspielen können? Der Kleb- und Dichtstoffhersteller Kömmerling zeigt auf der glasstec 2016 ein originales Teilstück aus einer medialen Glasfassade, das nicht nur bunte Bilder erzeugt, sondern sich auch interaktiv nutzen lässt. Für dieses Fassadenelement hat Kömmerling in Zusammenarbeit mit seinem südkoreanischen Partner G-SMATT Global Co ein Gießharz zum Einbetten von LEDs in Verbundglas entwickelt. Das G-Smatt Glass weist praktisch die Transparenz von Standard-Isoliergläsern auf und lässt sich als konstruktives Bauelement in Glasfassaden einsetzen. So macht es die bisherigen Kompromisse medial genutzter Fassaden zwischen Konstruktion, Transparenz und Effizienz überflüssig.
Gebäudefassaden werden seit ewigen Zeiten als Werbeflächen genutzt. Durch die Jahrzehnte sind die Techniken immer raffinierter geworden – vom einfachen Papierplakat über bunte Neonreklame aus gebogenen Glasröhren und Laufschriften bis hin zu übergroßen Monitoren und LED-Konstruktionen. Als aufgesetzte oder vorgehängte Elemente, die nur Teile der Fassade bedecken, waren sie bisher mehr oder weniger losgelöst vom „Werbeträger“. Zudem mit dem unerwünschten Nebeneffekt, das Tageslicht im Gebäudeinneren manchmal einzuschränken oder sogar komplett abzuschirmen.
Dagegen sind Displays, die als konstruktives Bauelement einer Fassade in die Gebäudestruktur integriert werden, mit der Architektur untrennbar verbunden. Mediale Plattform und Gebäudeform stehen in direktem Bezug zueinander, sie werden zur Medienarchitektur. Je nach dargestelltem Inhalt transportiert die Medienfassade über den reinen Werbezweck hinaus künstlerische oder architektonische Aspekte und tritt in Wechselwirkung mit ihrer Umgebung.
Konstruiert als Bauelement
Das von Kömmerling und G-SMATT entwickelte G-Smatt Glass ist Display und Bauelement zugleich: Das zwischen zwei Glasscheiben eingebettete LED-Raster kann mit beliebigem Inhalt angesteuert werden. Das Element selbst lässt sich wie ein Standard-Isolierglas verbauen und ist dadurch im Einsatz hoch flexibel. Bei Bedarf können die beiden Lichtebenen von medialer Darstellung und Innenraumbeleuchtung durch innenliegende Jalousien voneinander getrennt werden. „G-Smatt Glass ist ein hochentwickeltes Produkt, das drei Funktionen in einem Element verbindet: transparentes Glas, Media und Werbung und konstruktives Bauelement. Das kann keine andere LED-Fassade“, erklärt Chris Davis, Produktmanager bei Kömmerling UK.
Die Verwendung von Glas, die minimale Größe der integrierten LEDs und das klare Gießharz erlauben den Medien-Bauelementen eine außerordentliche Transparenz. Das Tageslicht strömt ungestört in das Gebäudeinnere, gleichzeitig wird die Durchsicht nach außen bei abgeschalteten LEDs nicht beeinträchtigt. Davis sagt: „G-Smatt Glass sieht aus wie normales Glas, bis es zum Entertainment wird. Dann verwandelt es sich in eine aktive Fassade. Die volle Media-Funktionalität in konstruktiven Glaselementen wird das Gesicht der Architektur und der Werbung verändern.“
Der medialen Darstellung sind nahezu keine Grenzen gesetzt. Farben, Bewegungssequenzen, Werbung, ganze Filme, interaktive Kommunikation mit Sensoren z.B. für Bewegung, personalisierte Inhalte, die Kopplung mit dem Internet – alles ist möglich.
Fertigung mit Robotergesteuerten Lasern
Die Entwicklungsarbeit für das G-Smatt Glass begann im April 2013 und fand sowohl in G-SMATT’s Entwicklungszentrum in Südkorea, als auch in der Kömmerling eigenen Forschungs- und Entwicklungsabteilung in Pirmasens statt. Für die Herstellung wird die hintere Scheibe zunächst mit einer metallenen und gleichzeitig transparenten Oberfläche versehen, um die notwendige elektrische Leitfähigkeit zu erzeugen. Robotergesteuerte Laser entschichten die Oberfläche anschließend nach Plan und legen so ein Raster aus feinen Leiterbahnen an. Auf dieses Raster werden die LEDs mit Hilfe eines elektrisch leitfähigen Klebstoffs im vorgesehenen Rasterabstand gesetzt und fixiert. Generell betragen die Rasterabstände 60mm, aber auch weitere Abstände sind möglich, um eine andere Auflösung zu erzielen. Je nach verwendeten LEDs ist das erzeugte Bild später entweder schwarz/weiß oder beliebig bunt.
Nachdem die zweite Glasscheibe im Abstand von 1,5 bis 2,5 mm auf die LED-Scheibe aufgesetzt ist, wird der Zwischenraum mit dem Gießharz Ködilan GS-LED aufgefüllt und danach unter UV-A-Licht gehärtet. Das einkomponentige Gießharz ist absolut transparent, maschinell applizierbar und besonders flüssig. So wird sichergestellt, dass das Harz alle Zwischenräume erreicht und sämtliche LEDs vollständig umschließt. Durch die Firmenpartnerschaft zur Entwicklung des LED-Verbundglases ist die Kompatibilität zu den weiteren in der Herstellung verwendeten Baumaterialien wie beispielsweise der Metallbeschichtung und des Klebstoffs gewährleistet.
Die Anschlüsse für Stromzufuhr und LED-Steuerung können an der Seite durch den Randverbund gelegt werden. Das fertige Verbundglas lässt sich mit einer oder zwei weiteren Glasscheiben, Gasbefüllung und Randverbund zu einem effizienten Mehrfach-Isolierglas bis zu den Maßen 1,5 x 3m ausbauen. Durch ihre langlebige Konstruktion und ihre hohe UV-Stabilität können die LED-Verbundgläser in einer Vielzahl architektonischer Anwendungen integriert werden. Anwendung finden die Gießharz-Verbundgläser beispielsweise in Fenstern und Fassaden, aber auch an Balustraden, Aufzugtürmen, Rolltreppen oder Böden – wo immer Flachglas verbaut wird.
Verbesserte Energie- und Kosteneffizienz
LED-Leuchtmittel sind aufgrund ihres hohen Wirkungsgrades in punkto Energieverbrauch heute das Maß der Dinge. Bei Medienfassaden lässt sich der Stromverbrauch vor allem durch die Größe der aktiven Fläche und die Anzahl der Pixel beeinflussen. Aber entscheidend ist auch, ob der mediale Inhalt bei hellem Tageslicht oder sogar direkter Sonneneinstrahlung genügend sichtbar sein soll, denn hierfür wird ein Vielfaches der Helligkeit und der Energie benötigt. Gleichzeitig beeinflussen Produktions-, Reinigungs- und Erhaltungskosten die Effizienz einer Medienfassade. Seine spezielle Konstruktion verschafft G-Smatt Glass im Vergleich mit anderen Lösungen deutliche Vorteile: Die Herstellung von Verbundglas mit Gießharz ist ein bewährtes Verfahren, das in der industriellen Fertigung eingesetzt wird. Bei der Montage der Medienelemente wird ein Arbeitsgang gespart, da die Gläser sofort im Gebäude integriert sind. Die geschützte Lage der elektronischen Bauteile sorgt für eine hohe Lebensdauer auch unter extremen Klimabedingungen oder hoher Luftverschmutzung. Zudem lassen sich die Elemente so einfach wie normale Verglasungen reinigen, ohne zusätzlichen Aufwand. Zusätzlich zu seinem niedrigen Energieverbrauch der LED-Technologie weist das Verbundglas auch hervorragende sicherheitsrelevante Eigenschaften auf und kann optimiert werden, um die Schalldämmung zu verbessern.
In Asien wird das Glas bereits vielfach eingesetzt, beispielsweise in der Myungbo Art Hall in Seoul. Aber auch der europäische Markt soll jetzt mit der transparenten Medienfassade erobert werden.

Gießharz-Innovationen
Neben dem G-Smatt Glass zeigt Kömmerling zahlreiche weitere Einsatzfelder für Gießharze. Dazu zählen Funktionsgläser wie schusssicheres Glas oder besonders schalldämmende und UV-schützende Gläser. Ebenso finden die Gießharze in bautechnischen Konstruktionen wie Balustraden oder Glasböden und im Schiffsbau Anwendung. Zusätzlich lassen sich Gießharz-Elemente für außergewöhnliches Glasdesign mit Dekoren oder Oberflächentexturen verwenden. Da die Gießharzprodukte von Kömmerling ohne hohe Temperaturen oder zusätzlichen Druck passiv aushärten, können Verbundgläser auch mit integrierten Materialien wie Kunststoff oder Stein besonders schonend hergestellt werden.
Die neueste Kömmerling Gießharzentwicklung zusammen mit Schollglas ist Ködistruct LG. Mit diesem aliphatischen Polyurethan werden Verbundgläser (GEWE-Composite®) mit herausragenden optischen und mechanischen Eigenschaften produziert. Damit sind merkliche Gewichtseinsparungen ohne Leistungseinbußen möglich und bedingt durch die exzellente Schubfestigkeit, können kaltgebogene Gläser durch Laminierung hergestellt werden. Des Weiteren wird für Ködistruct LG ein Materialgesetz auf dem glasstec-Kongress engineered transparency präsentiert, das es erlaubt, die Deformation von Verbundglaselementen in Abhängigkeit von der vorliegenden Last, der Temperatur und der Zeit zu bestimmen.
Kömmerling zeigt seine vielfältigen Kompetenzen für die Herstellung und Optimierung verschiedenster Funktionsgläser vom 20. – 23. September 2016 auf der Düsseldorfer glasstec in Halle 17 Stand C20.



Weitere Informationen und Belegexemplar an:
Kömmerling Chemische Fabrik GmbH
Zweibrücker Str. 200
66954 Pirmasens
Tel: +49 6331 56-2330
Fax: +49 6331 56-1110
E-Mail: alexandra.rohr@hbfuller.com
www.koe-chemie.de
Abstandhalter der nächsten Generation
Das thermoplastische Warme-Kante-System Ködispace 4SG von H.B. Fuller | KÖMMERLING wurde vom nordamerikanischen Adhesive and Sealant Council (ASC) mit dem ASC Innovation Award ausgezeichnet. Mit dem Abstandhalter der nächsten Generation überzeugt der weltgrößte Anbieter von Kleb- und Dichtstoffen für Isolierglasanwendungen seit 2016 auch die US-amerikanische Bauindustrie.
Anfang November 2020 verlieh das Adhesive and Sealant Council mit Sitz in Alexandria, Virginia (USA), zum vierten Mal seinen begehrten Innovationspreis. Mit dem ASC Innovation Award sollen Innovationen in der Kleb- und Dichtstoffindustrie und in der Wissenschaft gefördert werden. Eine unabhängige Jury prüft die eingereichten Lösungen unter anderem auf ihre Innovationskraft und die Auswirkungen der Technologie auf den Stand der Technik. H.B. Fuller | KÖMMERLING überzeugte die Juroren mit seinem thermoplastischen Abstandhalter Ködispace 4SG und wurde als Zweitplatzierter ausgezeichnet.
Das Adhesive and Sealant Council (ASC) ist ein nordamerikanischer Verband, der für die Kleb- und Dichtstoffindustrie eintritt. Er ist ein Zusammenschluss von über 100 Kleb- und Dichtstoffherstellern, Lieferanten, Händlern und Industrieberatern. Das ASC bietet seinen Mitgliedern eine Plattform für den Wissensaustausch, fördert Kooperationen für innovative Produktentwicklungen und vertritt die Branche als gemeinsame Interessenvertretung.
Ködispace 4SG überzeugt die Jury
Ködispace 4SG ist ein reaktiver thermoplastischer Abstandhalter zur Verwendung im Isolierglas. Als Warme-Kante-System der nächsten Generation vereint Ködispace 4SG Abstandhalter, Trockenmittel und primäre Dichtungsmasse in einem Produkt. Da sich Ködispace 4SG chemisch sowohl mit der Glasoberfläche als auch mit einer Silikonsekundärversiegelung verbindet, „verschmilzt“ der gesamte Randverbund zu einer sehr belastbaren Einheit. So entstehen dauerhaft dichte und extrem langlebige Isoliergläser. Ein weiterer großer Vorteil ist die Flexibilität von Ködispace 4SG: Es kann Verformungen aufnehmen, ohne dass dabei signifikante Spannungen im Randverbund erzeugt werden. Das prädestiniert das Warme-Kante-System speziell für mechanisch anspruchsvollere Anwendungen wie etwa das Kaltbiegen von Isolierglaseinheiten. Bei diesen Einsätzen weist es klare Vorteile gegenüber konventionellen, starren Abstandhaltern auf. Ködispace 4SG eignet sich für die Herstellung von Isolierglas für Standard-Fenster, aber auch für anspruchsvolle Structural-Glazing-Anwendungen.
„Wir freuen uns sehr, dass das Adhesive and Sealant Council das Potenzial von Ködispace 4SG erkannt und unsere Lösung ausgezeichnet hat“, sagt Dr. Christian Scherer, Head of Business Development Glass bei H.B. Fuller | KÖMMERLING. „Mit unserem Abstandhaltersystem sorgen wir nicht nur für ein energieeffizientes, langlebiges Isolierglas, sondern bieten Planern und Bauherren eine nahezu grenzenlose Designfreiheit und ermöglichen dadurch innovative Glaskonstruktionen. Bis heute wurden weltweit mehr als 15 Millionen Quadratmeter Isolierglaseinheiten mit Ködispace 4SG verbaut, die bei Tausenden von Wohn- und Geschäftsgebäuden – von kleinen Einfamilienhäusern bis hin zu riesigen Wolkenkratzern mit atemberaubender Architektur – eine langfristige Energieeffizienz erreichen und damit ihren Teil zur Bekämpfung des Klimawandels beitragen.“

Im fließenden Glasdach der Chadstone Mall in Melbourne sorgt das flexible Warme-Kante-System mit Ködispace 4SG bei den kaltgebogenen Isoliergläsern für dauerhafte Gasdichtigkeit.

Die Trophäe des ASC Innovation Award für das reaktive thermoplastische Abstandhaltersystem Ködispace 4SG

Aufgrund seiner speziellen Zusammensetzung geht Ködispace 4SG im Randverbund sowohl mit dem Glas als auch mit dem Sekundärdichtstoff Silikon eine chemische Bindung ein. Das Isolierglas wird so zu einer fest verbundenen und dennoch flexiblen Einheit.
Weitere Informationen und Belegexemplar an:
Kömmerling Chemische Fabrik GmbH
Zweibrücker Str. 200
66954 Pirmasens
Tel: +49 6331 56-2330
Fax: +49 6331 56-1110
E-Mail: alexandra.rohr@hbfuller.com
www.koe-chemie.de
Aktive Fassaden brauchen innovative Ideen
„Aktive Fassade“ lautet eines der wichtigsten Stichworte für die Architektur der Zukunft. In Zeiten der Debatten um Klimaschutz und nachhaltige Gebäudekonzepte hat sich die Glasfassade zu einem multifunktionalen und hochkomplexen Bauelement gewandelt. Sie erfüllt zahlreiche Aufgaben wie Wärme- und Schalldämmung, Sonnenschutz oder Lichtsteuerung. Inzwischen wird sie sogar zur Energiegewinnung sowie als mediale, interaktive Plattform eingesetzt. Der Dicht- und Klebstoffhersteller Kömmerling aus Pirmasens forscht intensiv und kontinuierlich an neuen Anwendungen und ist regelmäßig Partner bei innovativen Fassadenprojekten.
Die Integration der verschiedenen Technologien in die einzelnen Glaselemente erfordert ein Höchstmaß an Entwicklungs- und Ingenieurkompetenz. Auf diese Anforderungen hat sich Kömmerling Chemische Fabrik spezialisiert. Zu den Kompetenzen des Unternehmens zählt insbesondere der Randverbund im Structural Glazing. Mit dem Dichtstoff Ködispace 4SG ermöglicht der Hersteller ein Warme-Kante-System, das auf einzigartige Weise die Anforderungen silikonversiegelter Isolierverglasungen erfüllt. Denn der schwarze, auf Polyisobutylen basierende Abstandshalter haftet nicht nur mechanisch, sondern verbindet sich chemisch – und zwar sowohl mit dem Glas als auch mit dem Sekundärdichtstoff Silikon. Das heißt, Randverbund und Glas verschmelzen praktisch zu einer festen und zugleich elastischen Einheit. Die Vorteile liegen auf der Hand: Die Isolierglaseinheiten passen sich auch starken mechanischen Belastungen flexibel an und bleiben dadurch langfristig gasdicht. So gewährleistet der Randverbund selbst bei anspruchsvollen Anwendungen wie dem Montagebiegen von Isolierglaselementen dauerhafte Energieeffizienz und Funktionalität. Diesen Effekt hat Kömmerling durch Finite-Elemente-Simulationen und Berechnungen bereits in konkreten Bauprojekten nachgewiesen – zum Beispiel bei architektonischen Meisterleistungen im physikalischen Grenzbereich wie die EXPO-Pavillons in Kasachstan oder die Shoppingmall Chadstone im australischen Melbourne.
Die Fassade als Stromlieferant
Neben der Energieeffizienz ist die Energiegewinnung ein weiteres wichtiges Thema. Ähnlich den Isoliergläsern lassen sich auch Solarpaneele mit dem elastischen Randverbund von Kömmerling herstellen – als Glas-Glas-Modul TPedge, das etwa im Freiburger Fraunhofer Institut für Solare Energiesysteme getestet wird. Auftretende Pumpbewegungen der Gläser werden durch den flexiblen Randverbund ausgeglichen und das Modul hält auch unter extremen klimatischen Bedingungen zuverlässig und dauerhaft dicht.
In der Fassade integrierte Solarpaneele (Building Integrated Photovoltaik = BIPV) übernehmen heute schon einen Teil der Stromerzeugung. Voraussetzung für eine gestalterisch ansprechende Lösung ist unter anderem eine schlanke und dennoch stabile Befestigung. Statt herkömmlicher Stahlkonstruktionen wurde zum Beispiel bei dem Stuttgarter Züblin-Gebäude Z3 eine geklebte Photovoltaik-Fassade realisiert. Dank eines speziellen, lastabtragenden Silikonklebstoffs von Kömmerling fügen sich die Elemente ganz ohne mechanische Zusatzsicherung harmonisch in die Architektur ein. Da lastabtragende Verklebungen ohne jegliche ergänzende Haltevorrichtungen in Deutschland bisher nicht zugelassen sind, holte Kömmerling für die Konstruktion am fünfgeschossigen Z3 deshalb eine Zustimmung im Einzelfall (ZiE) ein.
Konstruktive Bauelemente als mediale Plattform
Schon Ende des 19. Jahrhunderts wurden Gebäudefassaden mit Hilfe von Leuchtreklamen als Werbeflächen genutzt. Mit Kömmerling lassen sich die medialen Plattformen direkt als konstruktives Bauelement in die Fassade integrieren. Das von Kömmerling und G-SMATT entwickelte G-Smatt Glas ist Display und Bauelement zugleich. Für dieses Fassadenelement hat Kömmerling eine Laminationstechnologie, also ein spezielles Liquid Composite zum Einbetten von LEDs in Verbundglas entwickelt. Das G-Smatt Glas weist praktisch die Transparenz von Verbundgläsern auf und lässt sich als konstruktives Bauelement in Glasfassaden einsetzen. So macht es die bisherigen architektonischen und optischen Kompromisse medial genutzter Fassaden zwischen Konstruktion, Transparenz und Effizienz überflüssig.
Eines der weiteren aktuellen Projekte, das Kömmerling in Zusammenarbeit mit Partnern der Branche für die aktive Fassade vorantreibt, sind schaltbare Gläser. Je nach Bedarf lassen sie Sonnenlicht und Wärme in das Gebäude herein oder schirmen sie ab. Ähnlich den bisherigen Innovationen ist auch dieses Mal ein qualitativ hochwertiges Ergebnis zu erwarten.




Weitere Informationen und Belegexemplar an:
Kömmerling Chemische Fabrik GmbH
Zweibrücker Str. 200
66954 Pirmasens
Tel: +49 6331 56-2330
Fax: +49 6331 56-1110
E-Mail: alexandra.rohr@hbfuller.com
www.koe-chemie.de
Im Rahmen eines Forschungsprojektes haben das Bauunternehmen Ed. Züblin AG und die KÖMMERLING CHEMISCHE FABRIK GMBH mit moderner Klebtechnologie Photovoltaikmodule ohne zusätzliche mechanische Sicherung in eine Fassade integriert.
Ab 2020 sollen alle Neubauten in den Mitgliedsstaaten der Europäischen Union so viel Energie erzeugen, wie sie verbrauchen. Um die strengen EU-Richtlinien umzusetzen, sind Photovoltaikanlagen gefragt, da sie gebäudenah erneuerbare Energie erzeugen und dabei emissions-, lärm- und wartungsarm sind. Der Nachteil bisheriger sogenannter Building Integrated Photovoltaics (BiPV): Die Standardisierung der Elemente macht eine individuelle Fassadengestaltung schwierig. Zudem wirken Rahmen und mechanische Befestigungen herkömmlicher Module optisch störend. Aber es sind auch ästhetisch ansprechende, maßgeschneiderte Lösungen möglich: Am Züblin Gebäude Z3 in Stuttgart konnte 2017 im Rahmen des EU-geförderten Forschungsprojektes "Construct PV" eine geklebte Photovoltaik-Fassade mit Siebdruckmuster realisiert werden. Dank eines speziellen, lastabtragenden Klebstoffs von Kömmerling fügen sich die Elemente ganz ohne mechanische Zusatzsicherung harmonisch in die Architektur ein. Die Installation der Photovotaik-Module an der Südfassade des Z3 war der Höhepunkt des Projekts "Construct PV", das bereits 2013 initiiert, und von der Ed. Züblin AG koordiniert wurde. Ziel war es, beispielhafte Anwendungen effizienter und kostengünstiger gebäudeintegrierter Photovoltaik für opake Flächen in der Gebäudehülle zu entwickeln. Das niederländische Architekturbüro UN-Studio entwarf dazu zunächst eine Musterfassade, mit bereits bestehenden Möglichkeiten der Gebäudeintegration. Eine der gezeigten Fassadentypen stellte die vorgehängte hinterlüftete Fassade dar - wie die des Bürogebäudes Z3 auf dem Züblin-Campus in Stuttgart.
Keine zusätzlichen Befestigungen
Das Z3 wurde 2012 nach Plänen von MHM architects aus Wien fertiggestellt. Als Niedrigstenergie-Gebäude ist es mit einem DGNB-Zertifikat in Gold ausgezeichnet. Charakteristisch für den Bau sind die vor- und zurückspringenden 18 Meter hohen Lisenen aus brettschichtverleimtem, unbehandeltem Lärchenholz, die zur Verschattung beitragen. Sie stehen im Kontrast zu dazwischen liegenden, dunkel wirkenden Fassadenstreifen, bei denen sich Fenster und graphitgraue Glasbrüstungen abwechseln. Die Brüstungen aus ESG-Scheiben wurden nach dem Structural-Glazing-Prinzip lastabtragend geklebt. Im Rahmen von Construct PV wurden sie auf der Südfassade gegen Glas-Glas-Photovoltaik-Module ausgetauscht - ebenfalls ganz ohne zusätzliche mechanische Befestigung.
Zustimmung im Einzelfall
Ausschlaggebendes Regelwerk für Structural Glazing Fssaden ist die Europäische Technische Zulassung 002 (ETAG 002), sie unterteilt Fassadenkonstruktionen in vier Typen. Lastabtragende Verklebungen ohne jegliche ergänzende Haltevorrichtungen werden in der Leitlinie nach Typ IV geregelt. In Deutschland sind bisher nur Systeme mit mechanischem Eigengewichtsabtrag nach Typ I und II zugelassen, sodass eine Dauerbeanspruchung der Klebefuge grundsätzlich nicht zulässig ist. Für die Umsetzung der rein verklebten PV-Module am fünfgeschossigen Z3 musste deshalb eine Zustimmung im Einzelfall (ZiE) beantragt werden. Diese wurde durch einen speziellen Klebstoff und einen innovativen Aufbau der PV-Elemente erreicht. So steht die Frontscheibe der Glas-Glas-PV-Module seitlich über. Dieser Stufenaufbau erlaubt die unabhängige Verklebung der Front- und der Rückscheibe auf der Unterkonstruktion, sodass die Lastabtragung aufgeteilt wird.
Strukturelle Verklebung
Den passenden Klebstoff lieferte Kömmerling. Der Spezialist für hochwertige Kleb- und Dichtstoffe unterstützte zudem den Genehmigungsprozess durch rechnerischen Nachweis der notwendigen Klebefugen-Dimensionierung zwischen PV-Modul und Unterkonstruktion. Das Unternehmen verfügt über modernste Prüf- und Messtechnik, mit der die Produkte auf ihre Eigenschaften getestet werden können. Für die neue Photovoltaik-Fassade des Z3 kam das 2-K Structural Glazing Silikon Ködiglaze S zum Einsatz. Structural Glazing - strukturelle Verklebung - bezeichnet die Glasmontagetechnik wie sie beim Züblin-Bürogebäude umgesetzt wurde. Statische und dynamische Lasten auf der Außenfassade wie zum Beispiel Eigengewicht, Wind- und Schneelasten sowie thermische Ausdehnung werden dabei über die strukturelle Verklebung auf die Unterkonstruktion übertragen. Kömmerling Structural Glazing Silikone zeichnen eine hohe mechanische Festigkeit bei gleichzeitig hoher Elastizität aus. Für die gesamte etwa 240 Quadratmeter große Fassadenfläche des Züblin-Bürogebäudes wurden etwa 250 Kilogramm benötigt.
Insgesamt wurden an der Südfassade des Zübin-Bürogebäudes 186 Photovoltaik-Module in sechs verschiedenen Größen installiert. Die Fläche kommt auf eine Gesamtleistung von 30 kWp und soll einen elektrischen Ertrag von 17.000 kWh/Jahr liefern. Diese Ausbeute würde reichen, ein durchschnittliches Einfamilienhaus etwa ein halbes Jahr mit Energie zu versorgen. Die gewonnene Energie wird in das Z3-Gebäude eingespeist. Wissenschaftlich erfasst und überwacht wird der Solarstrom-Ertrag vom Fraunhofer ISE.

Um die siebbedruckten PV-Module nur über eine Verklebung ohne zusätzliche mechanische Befestigung über acht Metern Einbauhöhe montieren zu dürfen, war eine Zustimmung im Einzelfall notwendig. Kömmerling unterstützte beim Genehmigungsverfahren.
Foto: Ed. Züblin AG

Das Züblin-Bürogebäude Z3 wurde 2012 nach Plänen von MHM architects aus Wien fertiggestellt. Seit 2017 werden an der Südfassade lastabtragende Verklebungen von PV-Modulen getestet.
Foto: Ed. Züblin AG
Weitere Informationen und Belegexemplar an:
Kömmerling Chemische Fabrik GmbH
Zweibrücker Str. 200
66954 Pirmasens
Tel: +49 6331 56-2330
Fax: +49 6331 56-1110
E-Mail: alexandra.rohr@hbfuller.com
www.koe-chemie.de
Die Branche ist sich einig: Direct Glazing, das Kleben der Isolierglasscheibe in den Fensterrahmen, bestimmt die Zukunft des Fensterbaus, denn das Verfahren bietet viele Vorteile für Fensterbauer und deren Kunden. Spezialist in diesem Bereich ist der Klebstoffhersteller Kömmerling mit Sitz in Pirmasens. Das Unternehmen widmet sich seit Jahren unter anderem der Weiterentwicklung von Produkten für Direct Glazing-Anwendungen und bietet hier aufeinander abgestimmte Systemlösungen an. Gemeinsam mit H.B. Fuller, dem neuen Mutterkonzern, gilt Kömmerling zudem als größter Anbieter von Kleb- und Dichtstoffen für Isolierglasanwendungen weltweit.
Während in der Schweiz bereits bis zu 40% und in Österreich bis zu 60% der Fenster geklebt sind, geht auch in Deutschland der Trend immer stärker zur standardmäßigen Klebung der Isolierglaseinheit in den Rahmen, wie zum Beispiel im Fertighausbau. Inzwischen gibt es speziell für die Verklebung entwickelte Fensterprofile, aber auch bei herkömmlichen Profilen ist diese Verbindung möglich. Direct Glazing bietet gegenüber der Montage mit Glasleisten überzeugende Vorteile für Fensterbauer und Bauherren: Die Verbesserung der statischen Eigenschaften des Fensters führt zu filigraneren Rahmen sowie größeren Scheibendimensionen und damit mehr Lichteinfall. Ebenso positiv fallen die geringeren Produktionskosten auf, da sich Material-, Personal- und Fertigungsaufwand reduzieren. Für die Fensterbauer mindern sich zudem die Servicekosten inklusive Scheibentausch um bis zu 82%. Für Endverbraucher wiederum ist die Verringerung der Energiekosten im späteren Gebäudebetrieb durch einen besseren U-Wert relevant. Positiv bemerkbar machen sich hier auch die reduzierte Wartungsnotwendigkeit und der wirksamere Schallschutz.

Direct Glazing, das Kleben der Isolierglasscheibe in den Fensterrahmen, bestimmt die Zukunft des Fensterbaus, denn das Verfahren bietet viele Vorteile für Fensterbauer und deren Kunden
Verbesserter Einbruchschutz durch geklebte Fenster
Ein besonders gewichtiges Argument für Direct Glazing ist der verbesserte Einbruchschutz. Bei über 80% der Einbrüche in Ein- und Zweifamilienhäuser kommen die Einbrecher über das Fenster ins Haus, so die Zahl im Präventionsreport Mai 2016 der Stiftung Deutsches Forum für Kriminalprävention. Wer sich schützen möchte, sollte deshalb mindestens auf die Widerstandsklasse RC2 (resistance class 2) bei seinen Fenstern achten, rät die Kriminalpolizei. Dazu ist eine lückenlose Sicherheitskette aus Glasanbindung, Falzbereich und Wandanschluss vorgeschrieben, was im Normalfall eine Verschraubung oder Verklebung der Glasleisten bedeutet. Wird das Isolierglas allerdings direkt mit dem Rahmen verklebt, verschmelzen Glas und Flügel zu einer Einheit und es entfallen die Ansatzpunkte für das Aufhebeln am Glasanschluss. Um die Anforderungen an RC2/RC3 zu erfüllen, müssen dann auch Beschläge und Glasscheiben mit entsprechender Widerstandsklasse gewählt werden. Kömmerling bietet hierbei einen zusätzlichen Sicherheits-Service und stellt gemeinsam mit den Beschlagherstellern Prüfelemente her, mit denen die Erfüllung der Einbruchhemmung getestet werden kann.
Systemlösungen garantieren dauerhafte Verklebung
Erfolgreich ist eine Verklebung von Isolierglas jedoch erst dann, wenn alle miteinander in Kontakt stehenden Materialien harmonieren. Um die Verträglichkeit zu gewährleisten, bietet Kömmerling als einziger Klebstoffhersteller Systemlösungen aus Isolierglasdichtstoffen und Klebesystemen aus einer Hand an. Sie sind für Holz, Kunststoff und Aluminiumrahmen verwendbar. Je nach Profilsystem wird die Klebeposition Überschlag, Falzgrund oder Glaskante gewählt. Wie robust die geklebten Fenstersysteme sind, zeigt die Verlängerung der Garantie durch Kömmerling auf 10 Jahre. Diese gilt, sobald im Randverbund und auch bei den Klebeflächen vom Unternehmen hergestellte und empfohlene Produkte verwendet werden. Die Betriebe, die sich trotz der genannten Vorteile immer noch vor der Integration oder gar kompletten Umstellung ihres Fensterbaubetriebs auf Direct Glazing scheuen, unterstützt Kömmerling bei der Einbindung des Klebeprozesses in die bestehenden Produktionsabläufe – von der einfachen Handapplikation über die Misch- und Dosieranlage bis hin zum Vollautomaten.

Wird das Isolierglas direkt mit dem Rahmen verklebt, verschmelzen Glas und Flügel zu einer Einheit und es entfallen die Ansatzpunkte für das Aufhebeln am Glasanschluss.
Weitere Informationen und Belegexemplar an:
Kömmerling Chemische Fabrik GmbH
Zweibrücker Str. 200
66954 Pirmasens
Tel: +49 6331 56-2330
Fax: +49 6331 56-1110
E-Mail: alexandra.rohr@hbfuller.com
www.koe-chemie.de
Seit Oktober 2017 gehört die Royal Adhesives & Sealants-Gruppe inklusive der Kömmerling Chemische Fabrik GmbH zum amerikanischen Konzern H.B. Fuller. Fuller ist einer der führenden Klebstoffhersteller weltweit und möchte mit der Akquisition seine Kompetenzen und sein Portfolio im Bereich Kleb- und Dichtstoffe erweitern. Für Kömmerling ist das nicht der erste Eigentümerwechsel. Inwieweit der neue Zusammenschluss die Strategie und Ausrichtung des Kleb- und Dichtstoffherstellers aus Pirmasens im Segment Glas beeinflussen wird, berichtet Kömmerling-Geschäftsführer Bernd Helfrich im Zuge der glasstec.
Was hat sich seit dem Zusammenschluss mit H.B. Fuller für Ihre Kunden geändert?
Das lässt sich ganz klar beantworten: Es gibt keinerlei operative Veränderungen für unsere Kunden durch den Eigentümerwechsel. Kömmerling agiert genauso kundenorientiert und technologiestark wie zuvor. Darüber hinaus können wir jetzt mit den Kollegen von H.B. Fuller auf größere Ressourcen in einem globalen Team aus Vertrieb, Entwicklung und Service zurückgreifen. Die zusätzliche Vermarktung unserer Dichtstoffe durch die weltweite Vertriebsstruktur von H.B. Fuller eröffnet uns dabei neue Wachstumsperspektiven. Gleichzeitig bleiben unsere Produkte, unser Service und unsere Qualität auf dem anerkannt hohen Level. Auch die Ansprechpartner haben nach dem Zusammenschluss nicht gewechselt. Die Geschäftsbereichsleitung Glas wurde nach dem unfallbedingten Ausscheiden von Herbert Haas an Ernst Semar übergeben. Er setzt die langjährig erfolgreiche Arbeit von Herbert Haas mit seinem kompetenten Team in bewährter Weise fort.
Welche Rolle spielt Kömmerling jetzt in der Fuller-Gruppe?
Kömmerling ist ein innovativer Anbieter in den wachstumsstarken Branchen Isolierglas und Transport, wobei wir vor allem in Europa und Asien agieren. Diese Zukunftstechnologien und Märkte sind für H.B. Fuller besonders interessant. Denn Fuller ist, bezogen auf Nordamerika, ebenfalls ein starker Player im Isolierglasbereich. Doch erst mit unserem Know-how und unserem Produktportfolio wird Fuller zum weltweit größten und technologieführenden Dichtstoffanbieter in diesem Marktsegment. In dieser Struktur verantwortet Kömmerling kommerziell und technisch jetzt das weltweite H.B. Fuller | Kömmerling Isolierglasdichtstoffgeschäft. Unser Hauptstandort Pirmasens wurde dieser organisatorischen Entscheidung folgend zum globalen Kompetenzzentrum aufgewertet. Darüber hinaus wurde das europäische H.B. Fuller-Geschäft der Engineering Adhesives mit seinen Schwerpunkten Automobil, Transport und Electronics unter Kömmerling-Führung organisatorisch neu aufgestellt. Unser technologieorientierter, auf Innovation und Wachstum ausgelegter Geschäftsansatz, der Kömmerling schon viele Jahrzehnte prägt, setzt sich somit auch in der neuen H.B. Fuller-Konzernstruktur fort.
Warum übernimmt Kömmerling im Isolierglas die Führung und wie ist der Standort Pirmasens für die neue Aufgabe als globales Kompetenzzentrum aufgestellt?
Bahnbrechende Innovationen im Bereich Glas und Fassade haben immer wieder Ihren Ursprung in den technologisch hochstehenden europäischen Märkten, vielfach weltweit erfolgreich ausgerollt durch Global Player mit Sitz in Europa. In diesem Umfeld hat Kömmerling im Segment der Isolierglasdichtstoffe seit dem Ende der 60er Jahre mit seinem breiten Know-how und seiner starken Marke stetig seine globale Marktpräsenz ausgebaut.
Unser neuer Eigentümer schätzt insbesondere die hohe technologische Kompetenz für die Glasbranche am Standort Pirmasens. Dies hat zur Ernennung von Pirmasens zum globalen Kompetenzzentrum für Isolierglasdichtstoffe geführt. Eine hervorragend aufgestellte Forschungs- und Entwicklungsabteilung mit hochqualifizierten Chemikern und Ingenieuren sowie unseren versierten Anwendungstechnikern, die von Pirmasens aus weltweit agieren, begründen diese Entscheidung. Der weitere Ausbau des Standorts zum globalen Kompetenzzentrum mit neuester Technologie dient der Festigung der weltweit führenden Marktposition und sichert uns die langfristige Wettbewerbsfähigkeit.
Bereits während der letzten drei Jahre haben wir in Pirmasens und an unserem zweiten deutschen Standort Langelsheim 15 Mio. Euro investiert. Davon können wir jetzt gemeinsam mit Fuller profitieren. So wurde in diesem Jahr in Pirmasens ein neuer leistungsfähiger Kneter für Isolierglasdichtstoffe in Betrieb genommen. Ebenfalls gestartet wurde eine Logistikerweiterung auf einem nahegelegenen eigenen Gelände mit 17.000 m2 Fläche. In Langelsheim haben wir den Produktionsbereich Butyl erweitert, und am Hauptstandort neben weiteren Investitionen in Silo- und Produktionsanlagen zusätzlich neue Prüf- und Messtechnik angeschafft.
Was passiert mit den Produkten im Glasbereich?
Das unseren europäischen Kunden bekannt breite und leistungsfähige Produktprogramm verändert sich durch den Eigentümerwechsel nicht. Wir fertigen nach wie vor vollständig in Pirmasens und Langelsheim. Unsere Kunden dürfen also auch weiterhin voll und ganz auf bekannte Qualität und technischen Service vertrauen. Die innovative Weiterentwicklung unserer global einsetzbaren Produkte steuern wir aus Pirmasens. Dabei orientieren wir uns wie bisher an den Anforderungen unserer Kunden. Die vier Technologiethemen Warme Kante, Structural Glazing, Verbundglas und Fensterverklebung werden in der Entwicklung bei Kömmerling zukünftig den höchsten Stellenwert einnehmen.
Was sind die langfristigen Vorteile der neuen Unternehmensstrukturen für Kunden im Glasbereich?
Langfristig werden unsere Kunden von der Stärkung und dem Ausbau der deutschen Standorte profitieren. Denn damit verknüpft sind ein marktführendes, innovatives Produktsortiment und ein weltweiter Service. Darüber hinaus ergeben sich aus der globalen Vernetzung der Entwicklungsabteilungen und der jahrzehntelangen Expertise beider Unternehmen neue Synergien: Unser hohes Verständnis für die Prozesse der Glasindustrie in Kombination mit einer starken Entwicklungsabteilung versetzt uns in die Lage, die Produkte und Prozesse unserer Kunden ganz konkret zu verbessern und mit unserem Expertenwissen ein kompetenter Partner für neue Entwicklungen im Glasbereich zu sein. Unsere Begeisterung für die technologische Weiterentwicklung energieeffizienter Produkte spielt hier eine ebenso große Rolle wie die enge Zusammenarbeit mit Maschinen- und Materiallieferanten. Dabei sind wir immer bestrebt, die Trends der Branche und unserer Kunden zu erkennen und aufzugreifen.
Wie sieht die generelle Strategie von Fuller aus?
Bezogen auf die Akquisition von Royal/Kömmerling ist H.B. Fuller konsequent seiner Wachstumsstrategie gefolgt und vertieft damit die bereits vorhandene Expertise für hochwertige Kleb- und Dichtstoffanwendungen in stark wachsenden Märkten. Klebstoffverbindungen, die dazu dienen, das tägliche Leben zu vereinfachen sowie Produkte und Prozesse besser und sicherer zu machen, stehen dabei im Vordergrund. Dazu zählen insbesondere Spezialanwendungen in Branchen wie Elektronik, Hygiene, Medizin, Transport, Bau, Erneuerbare Energie, Verpackung und Holzverarbeitung. Die Akquisition von Royal/Kömmerling macht H.B. Fuller darüber hinaus zum weltgrößten Anbieter von Isolierglasdichtstoffen und Klebstoffen für kommerzielle Bedachungsanwendungen. Als Technologieführer in vielen Marktsegmenten verfügt das Unternehmen über 6.000 Mitarbeiter an 73 weltweiten Standorten. Mit dem erweiterten innovativen Produktportfolio, gepaart mit einem hervorragendem Service, verfolgt H.B. Fuller das strategische Ziel, seinen Kunden in den genannten Schlüsselmärkten zu einer höheren Wertschöpfung zu verhelfen. Ein erfahrenes globales Team von Kleb- und Dichtstoffexperten stellt sich mit hohem Engagement dieser permanenten Herausforderung.
Das Interview ist u.a. in der bauelemente bau, Ausgabe 11/18 zu lesen.

Bernd Helfrich, Geschäftsführer der Kömmerling Chemische Fabrik GmbH, sieht neue Wachstumsperspektiven durch den Zusammenschluss mit H.B. Fuller.
Weitere Informationen und Belegexemplar an:
Kömmerling Chemische Fabrik GmbH
Zweibrücker Str. 200
66954 Pirmasens
Tel: +49 6331 56-2330
Fax: +49 6331 56-1110
E-Mail: alexandra.rohr@hbfuller.com
www.koe-chemie.de
Ist Klebtechnik zu komplex für die Praxis? Jein, sagen unsere drei Experten und legen den Fokus auf den Mehrwert, der in dieser Technologie vor allem für Fassaden- und Fensterbauer liegt. Zum Thema sprach die Redaktion mit den drei Experten Dr. Wolfgang Wittwer (W), Antonius Beier (B) und Michael Merkle (M).

mit der Redaktion (v.l.n.r.): Antonius Beier
(Vertrieb),
Michael Merkle (Anwendungstechnik) und Dr. Wolfgang Wittwer (Laborleiter).
Warum ist der Anteil der verklebten Fenster in Deutschland noch immer überschaubar?
W: Die Klebetechnologie ist relativ komplex. Viele konventionell produzierenden Fensterbauer haben daher Hemmungen, einzusteigen. Gleichzeitig muss der Mehrwert der Technologie bei den Endkunden mit einem gewissen Aufwand vermittelt werden. Meiner Einschätzung nach gibt es einige Treiber, bei denen die Mehrwerte sichtbar werden: Das eine ist die Fertigungsoptimierung bei den Fensterbauern selbst, die durch diesen Re-Engineering-Prozess eine bessere Ablaufstruktur in ihre Prozesse einbringen. Und das zweite ist, in Kundenhinsicht, sicher die einbruchhemmende Verglasung. Die zugfeste Anbindung der Scheibe erreicht eine Performance, die mit konventionellen Methoden so nicht zu machen ist.
B: Im Bereich RC2/RC3- Konstruktionen ist Verklebung mehr oder weniger Standard. Ich sehe es wie Dr. Wittwer, das Problem liegt in der Marktstruktur in Deutschland. Die Fensterbauer tun sich schwer, diese Technologie bei ihren Kunden erfolgreich zu vermarkten. Und das bremst den Prozess. Der Anteil der geklebten Fenster in Deutschland liegt etwa bei acht bis zehn Prozent. In Österreich und der Schweiz gehen die Uhren dagegen etwas anders: Wir gehen in Österreich von einem Anteil geklebter Fenster zwischen 50 und 60 Prozent und in der Schweiz von 30 bis 40 Prozent aus. In beiden Ländern gibt es Hersteller, die selbst auch Systemgeber sind. Das heißt, sie können die Vorteile der Klebetechnik argumentativ nutzen und sie können ihre Konstruktionen auf die Klebetechnik ausrichten.
W: Man kann das auch wirtschaftlich beleuchten: Für die Systemgeber ist es zunächst einmal eine Investition, die durch Vermarktungsargumente - zum Beispiel die Vermeidung von Stahl, um den U-Wert nach unten zu drücken - gerechtfertigt werden muss.
M: Mittlerweile erkennen viele aber den Trend. Inzwischen gibt es Klebeflügel von allen namhaften Systemgebern in Deutschland. Die meisten haben sich mit dem Thema also beschäftigt.
W: Bleibt die Frage, wie ich mich hinterher am Markt positioniere. Die Profilsystemgeber haben ihre Kunden, und auch die Kunden müssen den Weg mitgehen und können nicht einfach überrannt werden.



Es reicht nicht, dass alle Systemgeber Klebeflügel anbieten, um die Fensterbauer mitzuziehen?
W: Nein, dafür ist der Schritt einfach zu groß. Es gibt einfache Lösungen, bei denen zusätzlich geklebt wird. Um aber den vollen Nutzen zu erzeugen, wird der ganze Prozess vom Produkt her definiert. Dass der Prozess um die Aushärtung herum aufgebaut werden muss, war beim Fensterbauer in der Vergangenheit nicht gerade üblich. Das ist ein Schritt von der Manufaktur hin zu industrieller Fertigung.
Zusätzlich gibt es gewisse Ängste, die durch Probleme in der Anfangsphase der Klebetechnik geschürt worden sind. Diese Probleme entstanden durch eine nicht fachgerechte Umsetzung. Es ist nicht damit getan, einen Klebstoff zu finden, der an Glas oder Sekundärdichtstoff und am Rahmenmaterial Haftung hat. Hier gibt es mehr zu beachten - gerade in Bezug auf Verträglichkeit, aber natürlich auch zu Mechanik und Dauerbelastung von Verklebungen. Wenn man sich an die Richtlinien, die es zumindest zwischenzeitlich auch öffentlich gibt, gehalten hätte, dann wären diese Probleme allerdings gar nicht aufgetaucht.
B: Ein wichtiger Punkt ist die Angst der meisten Fensterbauer vor einem Scheibentausch vor Ort. Das ist verständlich - eine geklebte Scheibe ist anders zu entfernen als eine verklotzte. Aber erstens gibt es bei verklebten Fenstern viel weniger Scheibentausch und Scheibenbrüche, und zweitens kann jede verklebte Scheibe mit geringfügig höherem Aufwand getauscht werden. Die großen Fensterbauer sparen mit verklebten Fenstern bei den Servicekosten inklusive Scheibentausch zwischen 80 und 82 Prozent ein. Ein Argument, das für die Klebetechnik spricht.
Sind Schrägdachverglasungen durch Verklebungen auch bei einer Neigung von 2 Grad sicher?
Solange eine Klebung trocken bleibt, ist die Neigung kein Problem. Ähnliche Anforderungen führen wir seit langem im Fahrzeugbereich durch. Wichtig ist es daher, die Konstruktion einer Schrägdachverglasung dementsprechend auszulegen. Zum Beispiel, indem die Glasplatte von oben aufgesetzt wird und eine gute Drainage vorhanden ist. So lassen sich Dauerfeuchte und Verschmutzung an der Klebung vermeiden. Ebenso notwendig ist es, die Materialien aufeinander abzustimmen, damit sie mit der Klebung verträglich sind.
Was können Sie als Klebstoffhersteller tun, um die Fensterbauer zu überzeugen?
M: Eine wichtige Frage! Wir unterstützen gemeinsam mit den Profilsystemgebern die Fensterbauer vor Ort. Kömmerling bietet an, direkt in der Produktion Fensterelemente aus dem jeweiligen Betrieb mit dem Fensterbauer zusammen zu verkleben und das Ergebnis und die Stabilität mit herkömmlichen Fenstern zu vergleichen. Die praktische Überzeugung direkt vor Ort und nicht nur ein paar Vorteile auf dem Papier - das ist wichtig. Kömmerling stellt außerdem eigene Misch- und Dosieranlagen zur Einarbeitung beim Kunden vor Ort zur Verfügung. Oder wir zeigen die Verklebung in unserem neuen Technikum in Pirmasens.
Sie sagen also, die Praxiserfahrung ist der beste Weg?
W: Auf jeden Fall. Zwei Dinge sind wichtig: Sicherheit, dass die Klebetechnik etwas taugt - deswegen haben wir die RAL Güterichtlinien - und den Qualitätsunterschied erfahrbar und fühlbar zu machen.
M: Ein Fensterbauer muss außerdem nicht seine komplette Produktion umstellen, um zu kleben. Er kann sowohl Kle beflügel als auch konventionelle Flügelverarbeiten und das Kleben kann in den Produktionsprozess eingepasst werden. Von der einfachen Handapplikation über die Misch- und Dosieranlage bis hin zum Vollautomaten.
W: Im Prinzip gibt es diese Ad-On-Lösungen von ganz einfacher manueller Applikation bis zu kleinen Anlagen und dann schrittweise bis zur Automatisierung der kompletten Fertigungslinie. Es gibt also jede Menge Stufen dazwischen, bei denen Kömmerling auch mit Rat und Tat zur Seite steht. Wenn ich den Automatisierungsvorteil nutzen will, dann ist das ganz klar ein Re-Engineering, aber wenn ich meine Fertigungslinie behalten will, kann ich trotzdem kleben. Für den RC- Bereich gibt es eine ganze Reihe Firmen, die das so machen.
Kömmerling arbeitet mit pastösen Klebstoffen. Welche Unterschiede sehen Sie zum Klebeband?
W: Generell sind die mechanische Performance und die temperaturmäßige Bandbreite von Nasssystemen, egal welcher Couleur, breiter als die von Bändern.
M: Man muss bei dem Thema differenzieren und die Zusammenarbeit mit den Klebebandherstellern erwähnen. Das Klebeband wird teilweise als schnelle Fixierungshilfe gemeinsam mit dem Klebstoff verwendet. Wir arbeiten auch in verschiedenen Gremien zusammen, um die Verklebung voran zubringen.
W: Der Multimaterialmix kann viele Möglichkeiten eröffnen. Es gibt kein Entweder-Oder, sondern da lassen sich ganz clevere Kombinationen anbieten. Das gilt auch für andere Materialien im Fenster: Man kann zum Beispiel den Einsatz von Stahl und Verklebung mixen. Man hat optional die Möglichkeit, für sehr große geklebte Formate auch Stahl zu verwenden und bei kleineren Formaten den Stahl wegzulassen.
M: Das gilt entsprechend für dunkelfarbige oder anthrazitgraue Elemente, die sich viel schneller erwärmen.
Ist RC2/RC3 ebenfalls ein interessanter Ansatzpunkt?
M: Erfahrungsgemäß erkennen viele unserer Kunden, die wegen RC2/RC3 mit dem Kleben angefangen haben, die Vorteile, und stellen die Produktion komplett auf Kleben um. Bei geklebten Fenstern müssen für die Anforderungen an RC2/RC 3 nur noch die entsprechenden Beschläge und die Glasscheibe gewechselt werden. Kömmerling stellt gemeinsam mit den Beschlagherstellern Prüfelemente her, die beim Prüfinstitut getestet werden.
W: Leider treffen die Prüfungen nach europäischer RC2/ RC3-Norm keine Aussage über die Dauerhaftigkeit der Konstruktionen. RC2/RC3 sind rein mechanische Prüfvorschriften und, so sollen europäische Normen auch sein, designneutral. Das ist eine Quelle von Problemen, weil das ganze Thema Verträglichkeit hier nicht abgebildet wird. Es kann also sein, dass nach RC2/RC3 positiv geprüfte Fenster aufgrund schlechter Verträglichkeit der Werkstoffe im Feld versagen. Dann heißt es wieder „Das Kleben funktioniert nicht".
Wie unterstützt die RAL-Gütegemeinschaft das Thema Verklebung?
W: Unser erstes Ziel liegt natürlich beim Verbraucherschutz, indem wir dafür sorgen, dass er ein entsprechend langlebiges, abgesichertes Bauprodukt kaufen kann. Natür lich bietet dieser Schutz auch Sicherheit für die Fensterbauer. Deshalb haben wir mit der GZ 716 ein paar Verkehrsregeln aufgesetzt. Diese Richtlinie war das erste Regelwerk, bei dem man die Fragen nach der mechanischen Tauglichkeit der Klebstoffe und nach der Verträglichkeit aller Komponenten, die mit dem Klebstoff in Kontakt kommen, komplett berücksichtigt hat. Dies gilt sowohl für Klebebänder als auch für Klebstoffe. Das war schon ein Meilenstein.
Jetzt müssen wir schauen, dass wir das, was wir auf freiwilliger Basis in dem Zusammenschluss der Profilsystemgeber geschaffen haben, in den internationalen normativen Rahmen einbetten. Außerdem informieren wir den Markt über Veranstaltungen und natürlich über die Fachpresse.
Der wichtigste Pfad geht aber über die Mitgliedsfirmen der Gütegemeinschaft direkt an den Kunden.
Wann gibt es eine eigene europäische Norm?
W: Das kann ich im Augenblick noch gar nicht sicher sagen. Der Wille ist definitiv da, wir haben auch konkrete Schritte gemacht. Im ersten Quartal werden wir einen ersten Entwurf für ein Mandat ausformulieren, den wir dann auch noch zur Diskussion stellen müssen, bevor wir in den europäischen Ring steigen. Erfahrungsgemäß dauern die europäischen Prozesse allerdings ihre Zeit.
Quelle: Fassadentechnik 04/2017
Weitere Informationen und Belegexemplar an:
Kömmerling Chemische Fabrik GmbH
Zweibrücker Str. 200
66954 Pirmasens
Tel: +49 6331 56-2330
Fax: +49 6331 56-1110
E-Mail: alexandra.rohr@hbfuller.com
www.koe-chemie.de